DOI:
https://doi.org/10.14483/23448393.15681Published:
2020-10-02Issue:
Vol. 25 No. 3 (2020): September - DecemberSection:
Environmental EngineeringRecovery and Incorporation of expanded polystyrene SolidWaste in Lightweight Concrete
Recuperación e incorporación de residuos sólidos de poliestireno expandido en concreto liviano
Keywords:
Environmental pollution, lightweight concrete, polystyrene (R-PS), waste expanded polystyrene (en).Keywords:
Concreto liviano, contaminación ambiental, poliestireno (R-PS), residuos de poliestireno expandido (es).Downloads
References
K. Marsh and B. Bugusu, “Food Packaging Roles, Materials, and Environmental Issues”. Journal of Food Science, vol. 72, no. 3, pp. R39–R55, 2007. https://doi.org/10.1111/j.1750-3841.2007.00301.x
A. Ammala et al., “An overview of degradable and biodegradable polyolefins”, Progress in Polymer Science, vol. 36, no. 8, pp. 1015–1049, 2011. https://doi.org/10.1016/j.progpolymsci.2010.12.002
A. Cáceres, M. Sánchez-Soto, L. Maspoch, M. Sánchez-Hernández and A. Sánchez-Rojo, “Desarrollo de un Proceso de Reci-claje para la Fracción Mixta de Residuos de Plástico, Provenientes de Plantas de Separación Selectiva”, in II Congreso UPC Soste-nible, Barcelona, 2015.
S. Ross and D. Evans, “The environmental effect of reusing and recycling a plastic-based packaging system”, Journal of Cleaner Production, vol. 11, no. 5, pp. 561–571, 2003. https://doi.org/10.1016/S0959-6526(02)00089-6
C. H. Quintero-Peña, “Reciclaje termo - mecánico del poliestireno expandido (Icopor), como una estrategia de mitigación de su impacto ambiental en rellenos sanitarios”, M.S. thesis, Universidad de Manizales, Manizales, 2013.
Revista Semana, “¿Por qué cada vez más ciudades prohíben el icopor?”. [Online]. Available: https://www.semana.com/vida-moderna/articulo/por-que-cada-vez-mas-ciudades-prohiben-el-poliestireno/433365-3
I. Junca, “El icopor, una amenaza ambiental creciente para Bogotá”. [Online]. Available: https://www.elespectador.com/noticias/bogota/el-icopor-una-amenaza-ambiental-creciente-para-bogota/
L. Lizarazo, “Polémica por proyecto de ley que quiere prohibir el icopor”. [Online]. Available: https://www.portafolio.co/negocios/el-proyecto-de-ley-que-busca-prohibir-el-uso-del-icopor-508827
S. Angulo, “ICOPOR: El útil material que está lleno de problemas”. [Online]. Available: https://www.enter.co/cultura-digital/ciencia/icopor-el-util-material-que-esta-lleno-de-problemas/
M. Martínez, “Proyecto de Ley 2017: Por medio del cual se prohíbe la utilización del poliestireno expandido (icopor) en acti-vidades de comercialización de alimentos, se ordena la implementación de un Plan Nacional de Reciclaje del Icopor de uso indus-trial y se dictan otras disposiciones”. [Online]. Available: http://leyes.senado.gov.co/proyectos/index.php/textos-radicados-senado/p-ley-2017-2018/845-proyecto-de-ley-005-de-2017
J. Sierra-Pérez, I. López-Forniés, J. Boschmonart-Rives and X. Gabarrell, “Introducing eco-ideation and creativity techniques to increase and diversify the applications of eco-materials: The case of cork in the building sector”, Journal of Cleaner Produc-tion, vol. 137, pp. 606–616, 2016. https://doi.org/10.1016/j.jclepro.2016.07.121
J. K. Prusty, S. K. Patro and S. S. Basarkar, “Concrete using agro-waste as fine aggregate for sustainable built environment – A review”, International Journal of Sustainable Built Environment, vol. 5, no. 2, pp. 312–333, 2016. https://doi.org/10.1016/j.ijsbe.2016.06.003
B. S. Thomas and R. Chandra, “Properties of high strength concrete containing scrap tire rubber”, Journal of Cleaner Produc-tion, vol. 113, 2016. https://doi.org/10.1016/j.jclepro.2015.11.019
N. D. Gil-Jasso et al., “Dissolution and recovery of waste expanded polystyrene using alternative essential oils”, Fuel, vol. 239, pp. 611–616, 2019. https://doi.org/10.1016/j.fuel.2018.11.055
J. A. Rossignolo, M. V. Agnesini and J. A. Morais, “Properties of high-performance LWAC for precast structures with Brazil-ian lightweight aggregates”, Cement and Concrete Composites, vol. 25, no. 1, pp. 77–82, 2003. https://doi.org/10.1016/S0958-9465(01)00046-4
Y. Ke, S. Ortola, A. L. Beaucour and H. Dumontet, “Identification of microstructural characteristics in lightweight aggregate concretes by micromechanical modelling including the interfacial transition zone (ITZ)”, Cement and Concrete Research, vol. 40, no. 11, pp. 1590–1600, 2010. https://doi.org/10.1016/j.cemconres.2010.07.001
J. Yoon, J. Kim, Y. Hwang and D. Shin, “Lightweight Concrete Produced Using a Two-Stage Casting Process”, Materials (Ba-sel), vol. 8, no. 4, pp. 1384–1397, 2015. https://doi.org/https://dx.doi.org/10.3390%2Fma8041384
A. Ardakani and M. Yazdani, “The relation between particle density and static elastic moduli of lightweight expanded clay ag-gregates”, Applied Clay Science, vol. 93–94, pp. 28–34, 2014. https://doi.org/10.1016/j.clay.2014.02.017
Q. Du, Q. Sun, J. Lv and J. Yang, “Use of Preplaced Casting Method in Lightweight Aggregate Concrete”, Adv. Mater. Sci. Eng. vol. 2017, 2017. https://doi.org/10.1155/2017/7234761
M. Barbuta, R. D. Bucur, S. M. Cimpeanu, G. Paraschiv and D. Bucur, Wastes in Building Materials Industry. IntechOpen, 2015. https://doi.org/10.5772/59933
M. Barbuta et al., “Combined Effect of Fly Ash and Fibers on Properties of Cement Concrete”, in The 10th International Conference INTER-ENG 2016, Rumania, 2016.
J. Bolden, T. Abu-Lebdeh and E. Fini, “Utilization of recycled and waste materials in various construction applications”, American Journal of Environmental Sciences, vol. 9, no. 1, pp. 14–24, 2013. https://doi.org/10.3844/ajessp.2013.14.24
V. Gregorova, M. Ledererova and Z. Stefunkova, “Investigation of Influence of Recycled Plastics from Cable, Ethylene Vinyl Acetate and Polystyrene Waste on Lightweight Concrete Properties”, Procedia Engineering, vol. 195, pp. 127–133, 2017. https://doi.org/10.1016/j.proeng.2017.04.534
Instituto Nacional de Vías [INVÍAS], “Resistencia a la compresión de cilindros de concreto, I.N.V. E – 410 – 07”, INVÍAS, 2012.
Instituto Nacional de Vías [INVÍAS], “Porcentaje de partículas fracturadas en un agregado grueso, I.N.V. E – 227 – 13”, IN-VÍAS, 2013.
Instituto Nacional de Vías [INVÍAS], “Determinación de la resistencia del agregado grueso al desgaste por abrasión utilizando el aparato Micro- Deval, I.N.V. E – 238 – 07”, INVÍAS, 2012.
R. Chang and W. College, Chemistry. Ciudad de México: McGraw Hill, 2002.
R. Demirboga and A. Kan, “Thermal conductivity and shrinkage properties of modified waste polystyrene aggregate con-cretes”, Construction and Building Materials, vol. 35, pp. 730–734, 2012. https://doi.org/10.1016/j.conbuildmat.2012.04.105
Y. Liu et al., “Dynamic response of expanded polystyrene concrete during low speed impact”, Construction and Building Materials, vol. 122, pp. 72–80, 2016. https://doi.org/10.1016/j.conbuildmat.2016.06.059
A. Kan and R. Demirboga, “A novel material for lightweight concrete production”, Cement and Concrete Composites, vol. 31, no. 7, pp. 489–495, 2009. https://doi.org/10.1016/j.cemconcomp.2009.05.002
C. A. Cadere et al., “Engineering properties of concrete with polystyrene granules”, Procedia Manufacturing, vol. 22, pp. 288–293, 2018. https://doi.org/10.1016/j.promfg.2018.03.044
K. Ganesh Babu and D. Saradhi, “Performance of fly ash concretes containing lightweight EPS aggregates”, Cement and Con-crete Composites, vol. 26, no. 6, pp. 605–611, 2004. https://doi.org/10.1016/S0958-9465(03)00034-9
V. Ferrándiz-Mas and E. García-Alcocel, “Durability of expanded polystyrene mortars”, Construction and Building Materi-als, vol. 46, pp. 175–182, 2013. https://doi.org/10.1016/j.conbuildmat.2013.04.029
B. Chen and J. Liu, “Mechanical properties of polymer-modified concretes containing expanded polystyrene beads”, Con-struction and Building Materials, vol. 21, no. 1, 2007. https://doi.org/10.1016/j.conbuildmat.2005.08.001
How to Cite
APA
ACM
ACS
ABNT
Chicago
Harvard
IEEE
MLA
Turabian
Vancouver
Download Citation
Visitas
Dimensions
PlumX
Downloads
Recibido: 17 de septiembre de 2020; Aceptado: 11 de diciembre de 2020
Abstract
Context:
The high consumption of parts made from expanded polystyrene (EPS) generates environmental problems when disposed. Due to its low density and the low possibility of being utilized in other applications after its disposal, it is necessary to generate an alternative for the recovery and application of this type of waste. This work aims to generate an alternative in the application of EPS waste, particularly as a coarse aggregate in the manufacturing of lightweight concrete.
Method:
This study used discarded EPS containers as raw material. The material was cleaned, crushed and subsequently reduced in volume by applying acetone, generating pieces of polystyrene (R-PS) to be applied as a coarse aggregate for the manufacturing of lightweight concrete in different proportions. In addition, the pieces were subjected to a chemical attack process in order to observe their behavior.
Results:
The results show the degree of volume reduction of the EPS pieces by using different acetone ratios, establishing the best degree of reduction (in volume) of this material. Likewise, chemical attack tests show the behavior of R-PS against different agents in R-PS samples. Meanwhile, the failure tests on different concrete samples determine the best R-PS ratio as coarse aggregate for the manufacturing of lightweight concrete.
Conclusions:
The data obtained in this study show that the application of acetone on EPSW samples reduces its volume by up to 55 %. Concrete failure tests show that an optimum P-RS addition value, to be used as an aggregate in the manufacturing of lightweight concrete, is 7 %. This improves its resistance to chemical agents and weight reduction without significantly reducing the mechanical properties of concrete.
Keywords:
Environmental pollution, lightweight concrete, polystyrene (R-PS), waste expanded polystyrene..Resumen
Contexto:
El alto consumo de piezas fabricadas con poliestireno expandido (EPS, por sus siglas en inglés) genera problemas ambientales al desecharse debido a su baja densidad y la baja posibilidad de ser utilizado en otras aplicaciones posteriores a su desecho, lo cual hace necesario generar una alternativa de recuperación y aplicación de este tipo de residuos. Este trabajo tiene como objetivo generar una alternativa en la aplicación de residuos de EPS, en este caso, como agregado grueso en la fabricación de concreto liviano.
Método:
Este estudio utilizó recipientes de EPS desechados como materia prima. El material fue limpiado, triturado y posteriormente reducido su volumen mediante la aplicación de acetona, generando piezas de poliestireno (R-PS) para ser aplicado como agregado grueso para la fabricación de concreto liviano en diferentes proporciones. Además, las piezas fueron sometidas a un proceso de ataque químico para ver su comportamiento.
Resultados:
Los resultados muestran el grado de reducción de volumen las piezas de EPS mediante el uso de diferentes relaciones de acetona, estableciendo el mejor grado de reducción (en volumen) de este material. Asimismo, las pruebas de ataque químico muestran el comportamiento del R-PS ante diferentes agentes en las muestras de R-PS y las pruebas de falla sobre las diferentes muestras de concreto determinan la mejor relación R-PS como agregado grueso para la fabricación de concreto liviano.
Conclusiones:
Los datos obtenidos en este estudio muestran que la aplicación de acetona sobre las muestras de EPSW logra reducir su volumen hasta en un 55 %. Las pruebas de falla en concretos muestran que un valor de adición de P-RS óptimo a utilizar como agregado en la fabricación de concreto liviano es del 7 %, mejorando su resistencia ante agentes químicos y reducción de peso, sin reducir las propiedades mecànicas del concreto de forma significativa.
Palabras clave:
Concreto liviano, contaminación ambiental, poliestireno (R-PS), residuos de poliestireno expandido..Introduction
One of the most consumed materials in the world is expanded polyethylene (EPS), used in various commercial and domestic applications. Due to its high chemical stability preventing the generation of odours or flavours, this material is widely used in food [1]. The chemical stability of the material prevents its degradation [2]. However, this material has a low percentage of recovery and is not recyclable. in addition, it presents a very low density, generating large volumes of non-biodegradable waste, which increases the cost of transport and storage, reduces the useful life of landfills and also generates environmental and health problems [3]-[5]. Colombia has generated various strategies for mitigation and prohibition in the use of EPS [6]-[9]. However, these strategies have had little acceptance by society, specifically the proposal of laws and regulations to prohibit the use of products made with this material and the non-use of reusable or biodegradable food containers [10]. This problem generates the need to establish an alternative use of EPS waste (EPSW).
There are several methods for recycling EPS for construction [11]- [13]. These methods are expensive, however and generate environmental effects. Some friendly methods which have been developed focus on the production of oils from EPSW. These processes, however, generate secondary hazardous waste that may have a greater impact than unchanged EPSW [14]. These solid wastes (with a higher density due to their compaction by the addition of methanol) please the reduction volumes conventionally occupied by this type of materials. Unfortunately, the final products continue to have a very low density, so their application is better served as an aggregate in the manufacturing of lightweight concrete, which generates up to 10% weight reduction.
In the manufacturing of lightweight concrete, the use of artificial light aggregates from solid waste favours the possibility of high-rise building construction and prefabricated structures [15]-[17] without significantly altering the properties of the material, while also maintaining the concrete elastic modulus withing specifications [16], [18] and a reasonable resistance level [17], [19]. Moreover, the application of solid waste and garbage in the manufacturing of concrete also provides a favourable solution for environmental protection [20], [21].
This work reports a simple and low-cost method for the recycling of EPSW and its implementation in the manufacturing of lightweight concrete. This develops a solid alternative for the recycling of these solid wastes. The tests in this study were carried out by dissolving EPSW in different weight ratios of acetone for the manufacturing of recovered polystyrene particles (R-PS). Recycled EPSW and R-PS were applied in different proportions as aggregate for the manufacturing of lightweight concrete and for conventional concrete samples.
Materials and experimental details
The raw material used in this study were EPS cups that were formerly used for hot drinks on a college campus. They were recovered from ecological points arranged in coffee stations at of the University of Boyacá, Colombia with coordinates 5°34’03, 86” N and 73°20’17, 23” W, located at 2775 m.a.s.l. The EPS cups were first cleaned to remove solid and liquid waste from food and beverages and then subsequently dried at 115°C until a constant material weight was obtained.
The collected EPS cups were taken through a manual size reduction process to obtain of 1-5 cm x 1-5 cm average size. The obtained EPSW pieces were dissolved in acetone at ratios of 0:.25, 0:.50, 0:.75, 1 and 1:5 g of EPSW per mL of acetone in order to obtain the R-PS. The behaviour of the samples was observed for one month in order to track changes in the volume of the material. The data obtained during the process were used to determine the best relationship which produces sand aggregates that will be added to the lightweight concrete samples. Subsequently, the samples of crushed EPSW and R-PS were exposed to solutions of 1M HCl, 1M HNO3, 1M Na (OH) and CH3COOH for a period of one week to determine their stability against chemical agents.
The crushed EPSW and R-PS samples were added in concrete mortars (10 cm in diameter and 20 cm high) with a 7, 14 and 28 percent volume of concrete, subject to undergo impact tests until a fracture of the pieces was initiated to recover all of the R-PS pieces, which were added to the concrete for visual inspection. Compression tests were performed using CONTROLS CUPTECH equipment, specified for compression rupture tests, maintaining a load capacity of 100 kN with data collection at intervals of 1 kN and at a speed of 0,2 to 0,3 s. Tests were performed for conventional concrete samples and concrete samples with the addition of both crushed EPSW and R-PS [22]. Additionally, the mechanical resistance of the dissolved EPSW and the conventional aggregate used in concrete was carried out by means of the Micro-Deval test on Dirimpex S.A.A. equipment, model H38721N. This was accomplished by applying 2 L of water and an abrasive load of 5 kg of steel-balls with a diameter of 9,5 cm [23], [24]. The tests were conducted over a period of 2 h at 100 rpm. Four replicates were performed for each trial in this study. The data obtained were averaged.
Results
Raw material
Figure 1 shows the amount of material collected in a period of six months within a university plant. Due to holiday periods within the academic period, there are weeks where a solid waste collection of EPS was not obtained. Similarly, the management of solid waste from the EPS is associated with secondary materials that must be removed prior to the proposed treatment of the EPSW. Figure 2 shows the percentage of materials associated with the EPSW during its disposal in this study
Figure 1: EPSW collected during an academic semester within the University of Boyacá, Colombia.
Figure 2: Weight percentage of solid waste generated within the University of Boyacá, Colombia, during an academic semester.
Table I shows the specific weight of the EPSW waste collected during one academic semester. The specific weight was obtained using a 2 L Beaker, adding the 1-5 cm x 1-5 cm EPSW samples, first without generating any compaction effort followed by manual compaction to two different loads, which generated a densification process [25].
Table I: Apparent density of EPSW collected during a semester without and with compaction process.
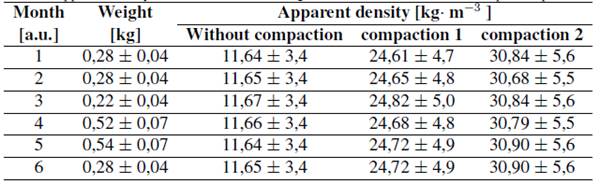
Next, the EPSW samples were subjected to a drying process in an electric oven at 1150°C until a constant weight of EPSW was obtained. The data obtained show a moisture percentage of 6.6% by weight. This percentage is mainly due to the remaining liquid deposited in the vessels after being cleaned. The data favours the formation and proliferation of microorganisms that can cause environmental and health problems [4].
EPS dissolution
Figure 3 shows the behaviour of the EPSW samples when dissolved with different acetone ratios. The images allow for observation of the physical behaviour obtained in the material (when subjected to acetone in different percentages). The acetone was observed at room temperature during a period of 30 days, where it naturally dispersed and disappeared over time. The best characteristics are observed on sample 4 (Figure 3-e) with a ratio of 1g of EPSW per mL of acetone. For the other ratios, the presence of porosities and irregularities (which could affect the performance of the material in concrete formulations) were observed.
Figure 3: Samples of EPSW dissolved in acetone with different weight ratios of EPSW/Acetone. In a) undissolved EPSW, b) 0,25:1 ratio, c) 0,5:1 ratio, d) 0,75:1 ratio, e) 1:1 and f) 1.5:1 ratio.
R-PS characterization
Table II shows the density variation of the EPSW before and after it was subjected to dissolution in acetone, as well as its behaviour when exposed to chemical agents.
Table II: Behaviour of the EPS and EP before exposure to chemical agents.

Application of EPS and R-PS in concrete
Tables III and IV show the relationships used for the manufacturing of conventional concrete and lightweight concrete with the addition of crushed EPSW and R-PS and the densities obtained for each of the manufactured samples. Figure 4 presents the data obtained in the compression test (on standard and concrete failed samples) with a 7, 14 and 28 percent volume addition of crushed EPS and R-PS for 7, 14 and 28 days of sample curing.
Table III: Material ratios for the concrete samples.
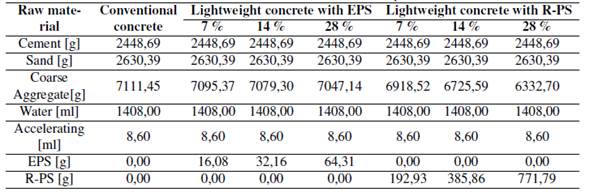
Table IV: Densities obtained for the concrete samples.

Figure 4: Compressive strength for the concrete samples.
Analysis
The results show that about a quarter of the weight of solid waste (collected in cafeterias of the university in a conventional academic period) corresponds to EPS cups used for hot drinks at the university. This represents 50% of the occupied volume of these materials in containers designated for the storage of solid waste within the university. This also demonstrates that the material is associated with other foreign materials, which hinders the recovery process of EPSW. However, as it can be seen in Table V, the compaction of the material inside the intended containers allows for the reduction of up to 28% of the volume occupied by discarded EPS cups (without any prior compaction process).
Table V: Volume occupied by solid wastes recovered from EPS before and after a process of compacting EPSW.
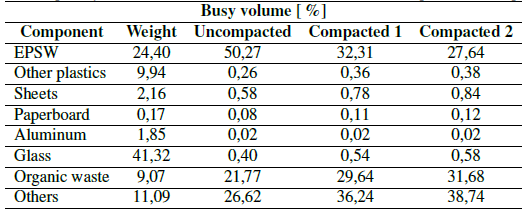
The dissolution of the EPS cups, with the addition of acetone, favours the compaction of these residues by means of a physicochemical process. This allows for the generation of a compact material without any need to apply forces in the process. However, the physical data obtained in the study show that the variation in the addition of acetone (for the material compaction process) physically affects the final product in its density and bubbles formation. Therefore, it can be observed that the best behaviour obtained is generated by a 1:1 ratio of EPSW pieces and acetone, obtaining a more homogeneous material without the presence of air cavities that can negatively affect the mechanical behaviour of the R-PS. Ultimately, this allows for greater use of EPSW during the previously stated process.
In addition, the data obtained show a variation in the specific weight samples of R-PS in relation to time, decreasing by 25,8 5% for a period of 30 days. Figure 5 shows the change in the mass of a sample of R-PS with a 1:1 ratio over a period of 30 days, as the acetone naturally evaporates at room temperature. A significant decrease in weight can be observed in the first 5 days, with a loss of 15 3% of its initial mass. This data corresponds to the presence of acetone as a remnant within the sample, deposited within the pores of the R-PS and delaying the process of the evaporation of acetone within the R-PS samples. This weight reduction can be taken into account for the process of utilising R-PS as coarse aggregate in the manufacturing of concrete. Specific consideration happens during the preparation of the raw material and applying drying times of the samples prior to their application.
Figure 5: Variation in time of the specific weight of EPSW dissolved in acetone.
Table II shows the variation in density and the fire behaviour for samples of crushed EPS and R-PS. A slight increase in the density of the material is observed when exposed in acetone, in addition to presenting a slow burning process in relation to the crushed EPS. Combustion tests showed that samples of crushed EPSW tend to disintegrate rapidly, generating a greater amount of airborne particles (or ashes), which can be considered pollutants due to incomplete combustion. This can be evidenced visually with the detachment of soot particles in the process, involving a risk for the environment [4]. Furthermore, it can also affect some structures that are made from it, which may come into contact with fire, resulting in a physical and mechanical change in the initial properties of this material [26].
Samples subjected to combustion processes have a combustion rate similar to that of crushed samples. However, R-PS samples have a longer burning time, a longer generation of solid waste after the process and more suspended particles. This allows the R-PS to have a greater applicability in its addition as a coarse aggregate in concrete, in relation to the EPSW, having a better behavior in the event of a fire. The addition of R-PS, combined with the addition of other solid plastic waste such as cable residues and ethylene vinyl acetate, favours an increase in the thermal conductivity and mechanical properties of the concrete. Therefore, the addition of other types of waste solids within the manufacturing of concrete would favour these properties [21].
The temperature stability data obtained at 180°C for a period of 5 min, show that the material presents a change in its physical appearance, forming a weak and fractured paste, in addition to a decrease in volume, which assumes an advantage for storage processes. The RPS samples submitted to this process show an expansion of their dimensions, increasing the volume without losing much of its properties. However, this characteristic can have negative consequences, due to the possibility of cracking in materials and structures where it is applied because of extreme thermal changes. These are unlikely to be obtained in a conventional event such as a fire, because the material will not present a direct contact to the fire, which allows a greater resistance towards this type of conditions.
The data obtained from the impact resistance in concrete specimens, with the addition of crushed EPSW and R- PS, reflect that the application of crushed EPSW or R-PS in concrete does not show cracking (by absorbing much of the energy supplied within the sample) [27]. The thick aggregate, conventionally used for the manufacture of structural concrete, shows significant fractures due to impact resistance tests (Fig. 6). This characteristic, due to the lack of adhesion between the R-PS and the cement, allows the achievement of a better behaviour of the concrete before impact efforts. This favours the manufacturing of a lighter concrete as a result to the addition of EPSW as a lightweight aggregate [28], [29].
Figure 6: Concrete cracking after impact tests. Breakdown of conventional coarse aggregate grains is observed while the light R-PS aggregates do not show cracking.
The data obtained during the behaviour test of crushed EPSW and R-PS (before the exposure of chemical agents) demonstrates that the material exposed to solutions of acids and bases did not show significant physical changes or traces of disintegration by the material. This is because the material needs polar solvents such as acetone to generate a physical change or dissolution of the material. Therefore, this material has a good utility in the presence of highly corrosive chemical agents, with an optimal performance in the applications commonly used for concrete [30], [31].
The resistance tests of the aggregate show that 78,01 3,5% of the aggregate of R-PS has a significant percentage of fractured faces, while coarse aggregate samples (conventionally used in the manufactureing of concrete) have a high degree of cracked material with a value close to 94 4,2 %. This shows that the R-PS aggregate has a greater resistance to cracking and wear of the material compared to the thick aggregate conventionally used in the manufacturing of concrete, with an overall improvement of 21,09 5,3 %. Similarly, the abrasion test shows a loss of 3,43 1,4% by weight in the R-PS sample, while the conventional aggregate sample reflects a loss of 25,87 4,86% of the initial weight, indicating that the aggregate of R-PS has greater durability, allowing less wear in abrasive conditions. This allows for the presence of greater stability in the material within its application for the manufacturing of concrete and its application in extreme environments, with the presence of highly toxic or abrasive environments.
Compression tests were preformed on conventional concrete and dosed concrete specimens with 7, 14 and 28 percent crushed EPSW and R-PS, respectively, in periods of 7, 14 and 28 days of curing. The data obtained show that the samples of concrete dosed with 7% by volume of crushed EPSW and R-PS have a compressive strength similar to the conventionally used concrete samples, reaching a resistance close to 27 MPa, 21% 4% less than the data obtained for conventional concrete [18], [29], [32]. The addition of 14 and 28% by volume of EPSW, however, decreases the mechanical properties of the concrete by 72,5 8,5 and 82,6 9% respectively and 35,6 6 and 55,9 7% for concrete samples dosed with R-PS. This allows a premise to be established that an excessive addition in the volume of EPSW or R-PS within concrete drastically reduces the mechanical resistance of the material. It also means that, with low material dosages, there is a better behaviour of the concrete with the application of R-PS [33], [34]. The R-PS samples, used as coarse aggregate in the manufacturing of concrete, show poor adhesion with the cement. This is due to the physical characteristics of the material and this factor must be improved in order to obtain better mechanical strength. The application of 7% of R-PS in a cubic metre of concrete will use 27,3 kg of EPSW. This is equivalent to 455 m3 of this waste that would not go into a landfill.
Conclusions
As a general analysis of the results obtained from this study, the implementation of R-PS not only simulates the mechanical properties of concrete, but it also improves other properties such as resistance and corrosion by exposure to chemical and corrosive agents. The implementation of R-PS also enhances weight reduction during the manufacturing of the concrete, favouring the possibility that the application of R-PS as a coarse aggregate for the manufacturing of lightweight concrete is valid. However, an excessive application of R-PS as a dispenser in concrete affects the mechanical properties of the material, which is why a low percentage of R-PS application is recommended as a coarse aggregate for the manufacturing of lightweight concrete.
Furthermore, the addition of acetone in EPSW as a dissolving agent allows a volume reduction of the material by 55 %, which reduces the space conventionally required for storage inside sanitary landfills, thus increasing its useful life. In addition, the treatment of EPSW to obtain R-PS allows an application of this material to be generated. This favours the processes of the storage and disposal of solid EPSW, favouring the recovery and recirculation of these materials as an environmental remediation mechanism. A 7% application of R-PS, in particular, could reduce up to 455 m 3 occupied by this type of waste in landfills, taking into account calculations obtained from the occupied volume of EPSW without the application of acetone.
Referencias
License
Copyright (c) 2020 Nicolas Rojas-Arias, Laura Juliana Torres-Parra, María Paula Espinoza-Merchán , Pablo Miguel Coha-Vesga

This work is licensed under a Creative Commons Attribution-NonCommercial-ShareAlike 4.0 International License.
From the edition of the V23N3 of year 2018 forward, the Creative Commons License "Attribution-Non-Commercial - No Derivative Works " is changed to the following:
Attribution - Non-Commercial - Share the same: this license allows others to distribute, remix, retouch, and create from your work in a non-commercial way, as long as they give you credit and license their new creations under the same conditions.