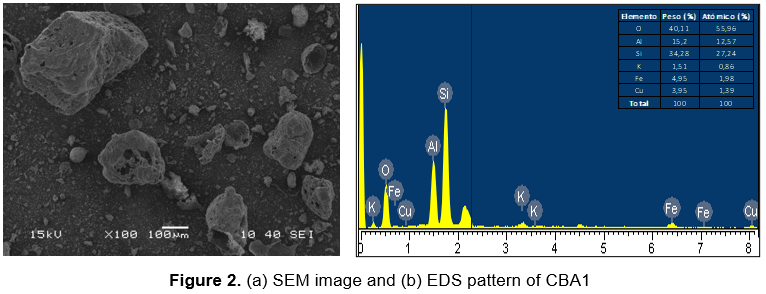
DOI:
https://doi.org/10.14483/23448393.19573Published:
2023-10-17Issue:
Vol. 28 No. 3 (2023): September-DecemberSection:
Environmental EngineeringStudy on the Use of Coal Bottom Ash as a Raw Material Replacement for the Production of Clay Bricks
Estudio sobre el aprovechamiento de cenizas de fondo de carbón como reemplazante de materia prima para la elaboración de ladrillos de arcilla
Keywords:
Bottom ash, building materials, industrial waste, sustainability (en).Keywords:
cenizas, materiales de construcción, residuos industriales, sostenibilidad (es).Downloads
References
Z. T Yao et al., “A comprehensive review on the applications of coal fly ash,” Earth-Sci. Rev., vol. 141, pp. 105-121, 2015. https://doi.org/10.1016/j.earscirev.2014.11.016 DOI: https://doi.org/10.1016/j.earscirev.2014.11.016
M. Temimi, J. P. Camps, and M. Laquerbe, “Valorization of fly ash in the cold stabilization of clay materials,” Resourc. Cons. Recyc., vol. 15, no. 3-4, pp. 219-234, 1995. https://doi.org/10.1016/0921-3449(95)00038-0 DOI: https://doi.org/10.1016/0921-3449(95)00038-0
M. Ilic, C. Cheeseman, C. Sollars, and J. Knight, J., “Mineralogy and microstructure of sintered lignite coal fly ash,” Fuel, vol. 82, no. 3, pp. 331-336, 2003. https://doi.org/10.1016/S0016-2361(02)00272-7 DOI: https://doi.org/10.1016/S0016-2361(02)00272-7
S. Jala and D. Goyal, “Fly ash as a soil ameliorant for improving crop production – A review,” Bioresource Technology, vol. 97, no. 9, pp. 1136-1147, 2006. https://doi.org/10.1016/j.biortech.2004.09.004 DOI: https://doi.org/10.1016/j.biortech.2004.09.004
Z. T. Yao, “Generation, characterization and extracting of silicon and aluminium from coal fly ash,” in Fly Ash: Sources, Applications, and Potential Environmental Impacts, P. K. Sarker, Ed., New York, NY, USA: Nova Science Publishers, 2013, p. 3-58.
E. Fidanchevski et al., “Technical and radiological characterization of fly ash and bottom ash from thermal power plant”, J. Radioanalytical Nuc. Chem., pp. 1-10, 2021. https://doi.org/10.1007/s10967-021-07980-w DOI: https://doi.org/10.1007/s10967-021-07980-w
S. A. Mangi, M. H. W. Ibrahim, N. Jamaluddin, M. F. Arshad, S. H. Khahro, and R. P Jaya, “Influence of coal ash on the concrete properties and its performance under sulphate and chloride conditions”, Environ. Sci. Poll. Res., vol. 28, no. 43, pp. 60787-60797, 2021. https://doi.org/10.1007/s11356-021-15006-x DOI: https://doi.org/10.1007/s11356-021-15006-x
P. K. Kolay and S. Bhusal, “Recovery of hollow spherical particles with two different densities from coal fly ash and their characterization”, Fuel, vol. 117, p. 118-124, 2014. https://doi.org/10.1016/j.fuel.2013.09.014 DOI: https://doi.org/10.1016/j.fuel.2013.09.014
W. J. Lee, J. S. Lee, D. Atarashi, Y. H. Kim, and S. H. Lee, “Pore structure and possibility of fine dust removal for bottom ash sand”, J. Korean Ceramic Soc., vol. 57, p. 378-384, 2020. https://doi.org/10.1007/s43207-020-00046-9 DOI: https://doi.org/10.1007/s43207-020-00046-9
E. Esmeray and M. Atıs, “Utilization of sewage sludge, oven slag and fly ash in clay brick production”, Const. Build. Mat., vol. 194, pp. 110-121, 2019. https://doi.org/10.1016/j.conbuildmat.2018.10.231 DOI: https://doi.org/10.1016/j.conbuildmat.2018.10.231
M. Sutcu, E. Erdogmus, O. Gencel, A. Gholampour, E. Atan, and T. Ozbakkaloglu, “Recycling of bottom ash and fly ash wastes in eco-friendly clay brick production”, J. Clean. Prod., vol. 233, pp. 753-764, 2019. https://doi.org/10.1016/j.jclepro.2019.06.017 DOI: https://doi.org/10.1016/j.jclepro.2019.06.017
M. Tripathi and V. B. Chauhan, “Evaluation of waste glass powder to replace the clay in fired brick manufacturing as a construction material”, Innov. Infras. Sol., vol. 6, no. 3, pp. 1-16, 2021. https://doi.org/10.1007/s41062-021-00492-2 DOI: https://doi.org/10.1007/s41062-021-00492-2
M. N. S. Zaimi, N. F. Ariffin, S. M. S. Mohsin, A. M. Hasim, and N. N. Nasrudin, “Behavior on the mechanical performance and scanning electron microscopy of coal waste brick”, Mat. Today: Proc., vol. 48, pp. 1816-1820, 2022. https://doi.org/10.1016/j.matpr.2021.09.136 DOI: https://doi.org/10.1016/j.matpr.2021.09.136
Zhang, L., “Production of bricks from waste materials – A review”, Const. Build. Mat., vol. 47, pp. 643-655, 2013. https://doi.org/10.1016/j.conbuildmat.2013.05.043 DOI: https://doi.org/10.1016/j.conbuildmat.2013.05.043
A. L. Murmu and A. Patel, A., “Towards sustainable bricks production: An overview”, Const. Build. Mat., vol. 165, pp. 112-125, 2018. https://doi.org/10.1016/j.conbuildmat.2018.01.038 DOI: https://doi.org/10.1016/j.conbuildmat.2018.01.038
I. Demir, “An investigation on the production of construction brick with processed waste tea”, Build. Environ., vol. 41, no. 9, p. 1274-1278, 2006. https://doi.org/10.1016/j.buildenv.2005.05.004 DOI: https://doi.org/10.1016/j.buildenv.2005.05.004
I. Demir, and M. Orhan, “Reuse of waste bricks in the production line”, Build. Environ., vol. 38, no. 12, p. 1451-1455, 2003. https://doi.org/10.1016/S0360-1323(03)00140-9. DOI: https://doi.org/10.1016/S0360-1323(03)00140-9
C. A. García-Ubaque, A. González-Hässig, and M. L. Vaca-Bohórquez, “Ceramic bricks made from municipal solid waste incineration-derived clay and ashes: A quality study”, Ing. Investig., vol. 33, no. 2, p. 36-41, 2013. https://doi.org/10.15446/ing.investig.v33n2.39515 DOI: https://doi.org/10.15446/ing.investig.v33n2.39515
C. Leiva et al., “Characteristics of fired bricks with co-combustion fly ashes”, J. Build. Eng., vol. 5, pp. 114-118, 2016. https://doi.org/10.1016/j.jobe.2015.12.001 DOI: https://doi.org/10.1016/j.jobe.2015.12.001
S. Abbas, M. A. Saleem, S. M. Kazmi, and M. J. Munir, “Production of sustainable clay bricks using waste fly ash: Mechanical and durability properties”, J. Build. Eng., vol. 14, pp. 7-14, 2017. https://doi.org/10.1016/j.jobe.2017.09.008 DOI: https://doi.org/10.1016/j.jobe.2017.09.008
ASTM C20-00, standard test methods for apparent porosity, water absorption, apparent specific gravity, and bulk density of burned refractory brick and shape for boiling water, ASTM International, West Conshohocken, USA, 2000.
NTC 4017, métodos para muestreo y ensayos de unidades de mampostería y otros productos de arcilla, Instituto Colombiano de Normas Técnicas y Certificación (ICONTEC), Colombia, 2018.
P. M. Velasco, M. M. Ortíz, M. M. Giró, and L. M. Velasco, “Fired clay bricks manufactured by adding wastes as sustainable construction material – A review”, Const. Build. Mat., vol. 63, pp. 97-107, 2014. https://doi.org/10.1016/j.conbuildmat.2014.03.045 DOI: https://doi.org/10.1016/j.conbuildmat.2014.03.045
D. Zuluaga, E. López, M. Pérez, and M. Correa, “Estudio de prototipos de ladrillos cerámicos elaborados con residuos de la minería del oro”, Rev. Col. Mat., vol. 15, pp. 51-63, 2020. https://doi.org/10.17533/udea.rcm.342056
J. Torres, L. F. Mosquera, P. Paz, and M. F. Díaz, “Evaluation of coal bottom ash for clay brick manufacturing: A preliminary study”, Rev. UIS Ing., vol. 20, no. 4, pp. 161-170, 2021. https://doi.org/10.18273/revuin.v20n4-2021013 DOI: https://doi.org/10.18273/revuin.v20n4-2021013
N. Afanador García, A. C. Ibarra Jaime, and C. A. López Durán, “Caracterización de arcillas empleadas en pasta cerámica para la elaboración de ladrillos en la zona de Ocaña, Norte de Santander”. Epsilon, vol. 1, no. 20, pp. 101-119, 2013. https://ciencia.lasalle.edu.co/cgi/viewcontent.cgi?article=1178&context=ep
R. Rodríguez-Álvaro, B. González-Fonteboa, S. Seara-Paz, and E. J. Rey-Bouzón, “Masonry mortars, precast concrete and masonry units using coal bottom ash as a partial replacement for conventional aggregates”, Const. Build. Mat., vol. 283, art. 122737, 2021. https://doi.org/10.1016/j.conbuildmat.2021.122737 DOI: https://doi.org/10.1016/j.conbuildmat.2021.122737
N. Phonphuak, S. Kanyakam, and P. Chindaprasirt, “Utilization of waste glass to enhance physical-mechanical properties of fired clay brick”, J. Clean. Prod., vol. 112, pp. 3057-3062, 2016. https://doi.org/10.1016/j.jclepro.2015.10.084. DOI: https://doi.org/10.1016/j.jclepro.2015.10.084
S. M. Kazmi, S. Abbas, M. A. Saleem, M. J. Munir, and A. Khitab, “Manufacturing of sustainable clay bricks: Utilization of waste sugarcane bagasse and rice husk ashes”, Const. Build. Mat., vol. 120, pp. 29-41, 2016. https://doi.org/10.1016/j.conbuildmat.2016.05.084 DOI: https://doi.org/10.1016/j.conbuildmat.2016.05.084
A. R. Djamaluddin, M. A. Caronge, M. W. Tjaronge, and R. Irmawaty, “Fired clay bricks incorporating palm oil fuel ash as a sustainable building material: An industrial-scale experiment”, Int. J. Sust. Eng., pp. 1-13, 2020. https://doi.org/10.1080/19397038.2020.1821403 DOI: https://doi.org/10.1080/19397038.2020.1821403
How to Cite
APA
ACM
ACS
ABNT
Chicago
Harvard
IEEE
MLA
Turabian
Vancouver
Download Citation
Recibido: 28 de junio de 2022; Revisión recibida: 17 de febrero de 2023; Aceptado: 9 de mayo de 2023
Abstract
Context:
Masonry bricks are one of the most widely used building materials in the world, which leads to the overexploitation of its raw materials. Its production consumes a large amount of energy and has a large environmental footprint. The clay brick industry can add residues to its raw materials; among those reported are tea processing waste, brick waste, paper industry residues, waste from coffee mills, and coal ashes.
Method:
Bottom coal ashes were characterized by X-ray fluorescence, X-ray diffraction, thermogravimetric analysis, electronic microscopy, and particle size analysis. In addition, their density and loss on ignition were determined. The incorporation of ashes in the elaboration of clay bricks was evaluated, with sand replacement percentages of 0, 3, 5, and 7 %. Finally, the physical and mechanical properties of the bricks were evaluated.
Results:
The water absorption and apparent porosity increased, while the compressive strength and bulk density decreased with the incorporation of ash in the brick samples, except for those with a 3% replacement, which showed a better performance in the evaluated properties.
Conclusions:
Coal bottom ashes have great potential in the manufacturing of clay bricks. The findings of this study indicate that, by incorporating up to 3% ashes, bricks can be obtained which comply with the Colombian regulations.
Keywords:
Bottom ash, building materials, industrial waste, sustainability.Resumen
Contexto:
El ladrillo de mampostería es uno de los materiales de construcción más utilizados en todo el mundo, lo que conlleva a una sobreexplotación de sus materias primas. Su producción consume gran cantidad de energía y tiene una gran huella ambiental. La industria de ladrillos de arcilla tiene la capacidad de adicionar residuos a su materia prima; entre los reportados se encuentran residuos del procesamiento del té, residuos de ladrillo, residuos de la industria del papel, residuos del beneficio de café y cenizas de carbón.
Método:
Se caracterizaron cenizas de carbón de fondo por fluorescencia de rayos X, difracción de rayos X, análisis termogravimétrico, microscopía electrónica y análisis de tamaño de partícula. Además, se determinó su densidad y pérdida al fuego. Se evaluó la incorporación de cenizas en la elaboración de ladrillos de arcilla, con porcentajes de reemplazo de arena de 0, 3, 5 y 7 %. Finalmente, se evaluaron las propiedades físicas y mecánicas de los ladrillos.
Resultados:
La absorción de agua y la porosidad aparente aumentaron, mientras que la resistencia a la compresión y la densidad aparente disminuyeron con la incorporación de cenizas en las muestras de ladrillos, a excepción de aquellas con un reemplazo del 3 %, las cuales presentaron un mejor desempeño en las propiedades evaluadas.
Conclusiones:
Las cenizas de fondo de carbón tienen un gran potencial en la fabricación de ladrillos de arcilla. Los hallazgos de este estudio indican que, al incorporar hasta un 3% de cenizas, se pueden obtener ladrillos que cumplen la normatividad colombiana.
Palabras clave:
cenizas, materiales de construcción, residuos industriales, sostenibilidad.Introduction
Coal ash is a by-product of coal combustion in thermal plants. It is considered one of the most complex and abundant anthropogenic materials in the world 1. When this residue is not properly disposed of, it can cause contamination in soil and water 1-3. These ashes represent between 5 and 20% of the coal fed into the process and are divided into bottom ashes (BA) and fly ashes (FA), which represent 5-15 and 85-95% by total weight of ashes generated, respectively 1. BA refers to the thicker ashes that fall to the ground through air flows and are collected mechanically, while FA are finer particles captured through electrostatic or mechanical precipitators 4-6.
At a global level, during the last decades, studies on the disposal and use of these ashes have been carried out. For example, due to their chemical and mineralogical composition, they have been used for the production of concrete 7 and the coating of cenospheres 8, among others. It is worth mentioning that BA is less often recycled than FA 9. Currently, the coal ashes generated are not fully used and are stored in ash ponds, lagoons, or landfills 1,10.
On the other hand, masonry brick is one of the most widely used building materials in the world, with a global annual production of 1.391 billion units. The great demand for this material in the construction sector has generated an overexploitation of its raw materials 11; its production consumes a lot of energy 12-14 and leaves a significant environmental footprint 13,14.
The clay brick industry can add great amounts of waste to its raw material 15. Therefore, various studies out on the use of waste in the manufacturing of bricks have been carried. However, comercial production is limited due to the absence of standards and a slow acceptance by the industry 14.
The literature has reported the use of tea processing residues 16, brick residues 17, sewage sludge 18, and residual glass powder 12 for manufacturing bricks. Likewise, the use of coal ashes in the production of clay bricks has been studied.
11 evaluated the use of FA and BA as substitutes for clay in brick manufacturing at two burning temperatures: 950 and 1.050 °C. It was found that the bricks with BA exhibited higher compressive strengths than those that incorporated FA. Compressive strength did not have a significant influence on temperature. On the other hand, it was found that the heavy metals present in the ashes were immobilized in the structure of bricks. Finally, it was concluded that the addition of coal ash in brick manufacturing can reduce the environmental impact of using natural resources and generating waste.
19 replaced up to 80% of clay with FA, employing burning temperatures between 800 and 1.000°C. The results showed that the compressive strength and water absorption improved with increasing firing temperature. On the other hand, the compressive strength decreased with the increase in CV content, except for the burning temperature of 1.000 °C. The authors state that FA can be useful for the production of clay bricks.
In the work by 20, at an industrial level, FA were added to bricks (0-25 %) as a replacement for clay at a temperature of 800 °C. The authors found that the addition of up to 20% FA satisfies the mínimum performance requirements of bricks according to the Pakistan building code.
Based on the above, it can be stated that ashes from the combustion of coal can be used as an addition to the ceramic industry. Therefore, the objective of this work was to study the use of coal bottom ash as a replacement for raw materials in clay brick manufacturing.
Methodology
For this work, coal bottom ashes (CBAs) were obtained from a Colombian company dedicated to clay brick manufacturing. CBAs are generated during the burning process of ceramic bricks, which is carried out at a temperature of 850 °C in a tunnel-type furnace. In this specific case, the company uses bituminous carbon. This company generates approximately 10 tons of CBAs per month. The simples were collected for five days in a stable furnace regime. Two samples, CBA1 and CBA2, were selected for this study.
The ashes were characterized via X-ray fluorescence (XRF) in a Philips MagixPro PW- 2440 equipped with a Rhodium tube, with a maximum power of 4 KW. Via X-ray diffraction (XRD) using a PANalytical EMPYREAN, the sample was measured in a Bragg-Brentano optical configuration with a high-speed solid-state detector for data acquisition called PIXCEL. They were also analyzed by scanning electron microscopy (SEM) using a JEOL frame equipment (JSM 5910 LV) operated at an acceleration voltage of 20 Kv. A chemical composition analysis was performed using an X-ray energy dispersion spectrometer (EDS). A thermogravimetric analysis (TGA) was also performed under oxidizing conditions at an air atmosphere and a heating rate of 10°C/min, with temperature range of 25-1.000°C, in a Q600 TA Instrument. In addition, the particle size distribution was determined by sieving, density, and loss on fire.
Likewise, the particle size was determined by sieving the sand used for brick manufacturing.
The bricks were made at a laboratory with clay, chamotte (ground brick), sand, and bottom ash. For this study, sand was partially replaced with coal bottom ash (CBA1 and CBA2). Table I shows the proportions used to make the bricks. For manufacturing, the raw materials were mixed mechanically, and the amount of water added was adjusted until a malleable consistency was obtained. The bricks were dried at room temperature for one day, in order not to cause fractures during drying. Then, they were placed in an electric oven at 190 °C for 24 hours. Finally, the bricks were placed in a tunnel furnace for 24 h at 850 °C. It is worth mentioning that this last step was carried out in the company’s furnace, i.e., under real conditions regarding the burning process.
Table I: Composition of experimental bricks

Once the bricks were made, tests such as apparent porosity, apparent density, and specific gravity were carried out according to the ASTM C20 standard 21. Additionally, the compressive strength and water absorption were determined according to the NTC 4017:2015 standard 22. Five samples were used for each test.
Results and discusión
CBA characterization
The ashes evaluated have similar chemical and physical characteristics, as shown in Table II. Regarding their chemical composition, they are mainly composed of SiO2, Al2O3, and Fe2O3, which add up to 89,68 and 92,03% in weight for CBA1 and CBA2, respectively. To a lesser extent, the ashes have sulfur oxides and calcium, among others. For brick manufacturing, the literature suggests a SiO2 content (present in clays) of 50-60% 23. According to Table II, the amount of silica present in CBA2 is slightly higher than recommended. It should also be noted that silica can generate an increase in porosity 23. This indicates that, in terms of the silica content, coal ash can be used as a substitute for clay. On the other hand, the presence of Fe2O3, a compound related to the formation of hematite, can give the bricks a reddish color 24. Additionally, a loss on ignition of 22,81 and 16,65·% were observed for BA1 and BA2, respectively, which is due to unburned organic matter content.
Table II shows that CBAs have heavy metals in their composition, which could leach and cause negative impacts on the environment. Therefore, in a test carried out before employing the CBAs, they were found to be non-hazardous, since the leaching levels of metals of environmental interest (such as Pb, Se, Cr, Hg, and Cd) were below the maximum limit established by Colombian regulations for hazardous waste. In addition, the ecotoxicity test for Daphnia Pulex was applied, which reported a non-ecotoxic residue 25.
Fig. 1 shows the X-ray diffractogram for CBA1, which shows crystalline phases such as quartz (SiO2), hematite (Fe2O3), and anatase (Ti0,784O2), in addition to an amorphous structure. These results agree with the chemical composition of the ashes (Table II). Table III shows the semi-quantification of the crystalline and amorphous phases of the ashes, where quartz is the main component (51,7 %) followed by the amorphous phase (34,6 %). The quartz content can be used as a degreasing material 26 which corresponds to sand and chamotte in this specific case.
Figure 1: Diffractogram of CBA1. Q: quartz; H: hematite; A: anatase
Table II: Chemical composition and physical properties of CBAs

Considering the above, that is, due to its chemical and mineralogical composition, coal bottom ash can be used as a substitute for raw material in the manufacturing of clay products 25.
The morphology and chemical composition of CBA1 are shown in Fig. 2. The ashes exhibit irregular angular particles of different sizes, and some porous particles are contemplated. On the other hand, according to the EDS analysis, the ashes have SiO2 as the main component, as well as Al2O3 to a lesser extent. These results confirm those obtained in the XRF analysis.
Fig. 3 shows the size distribution of the ashes. The particle size was approximately 700 and 500 μm for CBA1 and CBA2, respectively. This difference may be related to the efficiency of the combustión process 25. Likewise, the sand used reported an average particle size of less than 200 μm (Fig. 3).
The thermogravimetric analysis of CBA2 is presented in Fig. 4. Note that the ash had a weight los of approximately 7,7% at 1.000 °C. The main weight losses, in the range from 450 to 650 °C, are related to the loss of unburned carbon present in the ashes 27.
Table III: Semi-quantification of the crystalline phases and the amorphous phase of CBA1

Figure 2: (a) SEM image and (b) EDS pattern of CBA1
Figure 3: Granulometric curve: (a) bottom ash and (b) sand
Figure 4: Thermogravimetric analysis of CBA2
Brick performance evaluation
Water absorption
Water absorption is one of the most important parameters in evaluating the durability of clay bricks 28. Fig. 5 shows the results for the bricks made with sand replacements of 3, 5, and 7% with CBA1 and CBA2. It is observed that, with the increase in the proportion of ashes, the water absorption becomes slightly higher, except for the bricks with 3% CBA1. On the other hand, the bricks that incorporated CBA1 at 5% and CBA2 at 7% reported the highest absorption with values of 18,27 and 19,56 %, respectively, when compared to the control bricks (16,23 %). This represents increments of 13 and 21% for the each of the samples, respectively. The NTC 4205-2:2019 for non-structural masonry (solid bricks) establishes that the average maximum water absorption of five pieces must be 17 %. The bricks that incorporated CBA1 at 3% and CBA2 at 5% meet this requirement.
Figure 5. : Water absorption of the brick samples
Apparent porosity
Fig. 6 shows the apparent porosity of the bricks, which increased with the incorporation of ashes. This agrees with previous studies where bottom ash was used for manufacturing clay bricks 11. The change in the porosity of the bricks may be related to the different particle sizes of the raw materials used 11. The highest porosities were observed in the bricks that incorporated CBA1 at 5% and CBA2 at 7 %, with values of 35,53 and 37,17 %, respectively, with respect to the control bricks (31,96 %). On the other hand, the bricks that incorporated CBA1 at 3% presented a porosity of 31,66 %, similar to that of the control sample.
The increased porosity of the bricks can be attributed to the high percentage of loss on ignition and the low content of fluxing agents present in the ashes 29. On the other hand, bricks with high porosities are lighter and have good insulation properties 29. It is important to mention that water absorption and apparent porosity are directly related.
Figure 6: Apparent porosity of the bricks
Apparent density
The apparent density of clay bricks is influenced by the specific gravity of the raw material, the manufacturing methods used, and the degree of combustion 28. This parameter indicates the weight of the bricks 11. Fig. 7 shows the apparent density of bricks with different proportions of CBA. Note that the samples with ashes generated a reduction in the bulk density, i.e., 1,80 g/cm3 for the control brick and up to 1,62 g/cm3 for the brick that incorporates CBA2 at 7 %. The decreased density in bricks that incorporate ashes has been reported in other studies 11,30. It can be said that there is an inverse correlation between water absorption/bulk porosity and bulk density.
Compressive strength
Fig. 8 presents the compressive strength of the brick samples. The results show a decrease with the increased incorporation of CBA1 and CBA2. This reduction may be related to the increase in the porosity of the bricks 11. Similar trends were reported in studies incorporating residues in clay brick manufacturing 11,29,30. On the other hand, the compressive strength of the sample with CBA1 at 3% (15,72 MPa) showed a slight increase compared to the control sample (14,61 MPa). The NTC 4205-2:2019 establishes that, for non-structural masonry (solid bricks) the average compressive strength of five pieces must be a minimum of 14 MPa. Therefore, the bricks that incorporated CBA1 at 3% meet this requirement. Moreover, the lowest compressive strength was reported by the CBA2 sample at 5% (10,9 MPa), which represents a reduction of approximately 25% with respect to the control sample.
The results of the tests presented in this research indicate that coal bottom ashes have great potential as a raw material in the production of clay bricks. In addition, it is important to highlight that the ashes used in this study, which come from a brick factory, do not require prior treatment to be used in this type of process, which constitutes an economic advantage. On the other hand, the use of this waste allows reducing the demand for sand, as well as mitigating or preventing the disposal of this waste in landfills or near the manufacturing sites, which translates into environmental advantages. Finally, we recommend continuing with future studies that allow scaling the production of bricks with CBA to an industrial level.
Figure 7: Apparent density of the bricks (g/cm3)
Figure 8: Compressive strength of the bricks
Conclusions
This study evaluated the incorporation of coal bottom ashes in the manufacturing of clay bricks. The ashes used were mainly composed of silica and aluminum oxides, with mineral phases such as quartz and hematite, in addition to a high amorphousness. According to these characteristics, the ashes can be used as degreasing material in the production of clay bricks.
Regarding the properties of the bricks, the absorption of water increased with the incorporation of ashes, which is why the bricks with CBA1 at 3% and CBA2 at 5% can be used for non-structural masonry according to the Colombian technical standards. The apparent porosity increased, while the apparent density decreased with the incorporation of coal bottom ashes into the brick samples. Hence, lighter bricks can be obtained.
The compressive strength decreased with the increasing coal ash content. However, the bricks that incorporated CBA1 at 3% showed a resistance of 15,72 MPa, which satisfies the requirement for non-structural masonry as established by the Colombian regulations.
This study shows that, for the evaluated waste, an up to 3% replacement of bottom ashes with sand can be used to obtain bricks that meet quality standards of Colombian regulations. The use of coal bottom ashes can reduce the consumption of natural resources for manufacturing clay-based bricks, in addition to reducing the volume of waste for final disposal, which constitutes environmental and economic benefits
Acknowledgements
Acknowledgments
The authors would like to thank Universidad Nacional de Colombia and C.I. LAGO VERDE S.A.S. for their support in the development of this study
References
License
Copyright (c) 2023 José Fernando Benítez-Vivas, Juan Pablo Gutiérrez-López, Janneth Torres-Agredo, Luisa Fernanda Mosquera-Idrobo, Miguel Fernando Díaz-Huertas

This work is licensed under a Creative Commons Attribution-NonCommercial-ShareAlike 4.0 International License.
From the edition of the V23N3 of year 2018 forward, the Creative Commons License "Attribution-Non-Commercial - No Derivative Works " is changed to the following:
Attribution - Non-Commercial - Share the same: this license allows others to distribute, remix, retouch, and create from your work in a non-commercial way, as long as they give you credit and license their new creations under the same conditions.