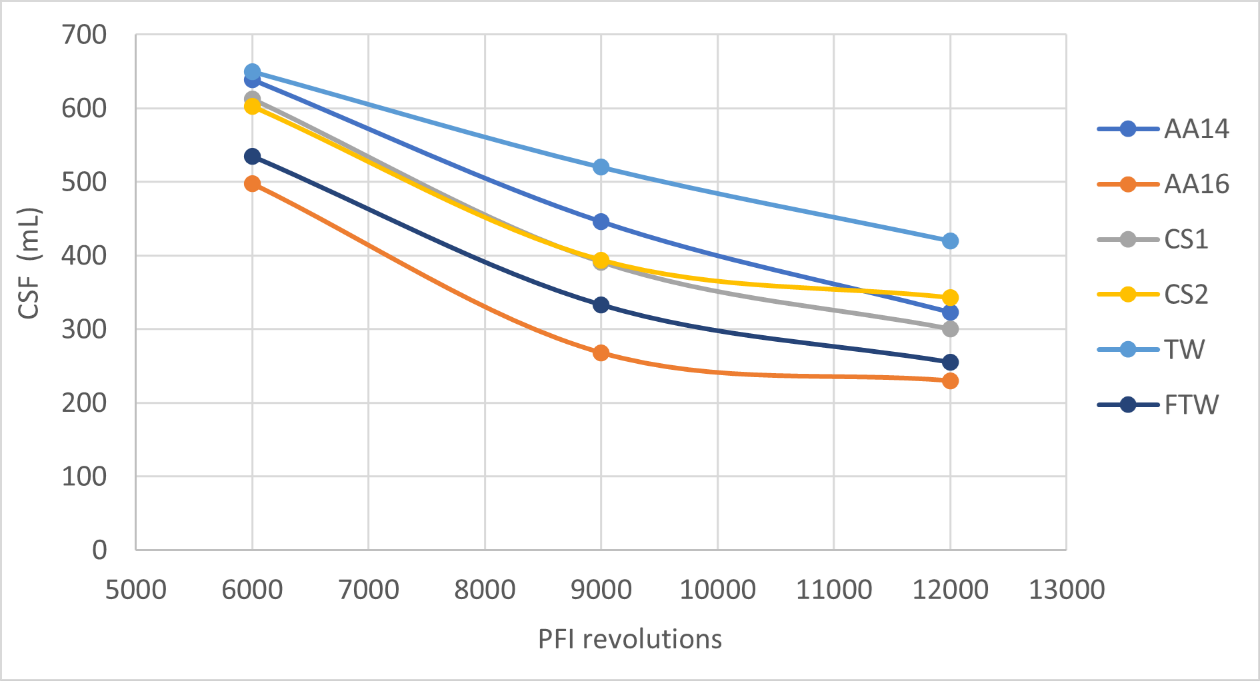
DOI:
https://doi.org/10.14483/23448393.21172Published:
2024-07-17Issue:
Vol. 29 No. 2 (2024): May-AugustSection:
Chemical, Food, and Environmental EngineeringDetermining the Pulping Conditions and Properties of Unbleached Pulp from Uruguayan Pinus Taeda
Determinación de las condiciones de pulpeo y propiedades de pulpa marrón a partir de Pinus taeda Uruguayo
Keywords:
kraft pulp, Paper properties, Pinus taeda (en).Keywords:
Pulpa kraft, Propiedades papeleras, Pino Taeda (es).Downloads
References
M. Boscana and L. Boragno (2018). “Estadísticas Forestales 2018,” Montevideo, Uruguay: Dirección General Forestal - Ministerio de Agricultura, Ganadería y Pesca. [Online] Available: http://www.mgap.gub.uy/sites/default/files/dgf_boletin_estadistico_2018_0.pdf
Uruguay XXI, “Informe del sector forestal en Uruguay,” 2016, [Online]. Available: http://www.uruguayxxi.gub.uy/inversiones/wp-content/uploads/sites/3/2014/09/Sector-Forestal-Uruguay-XXI-2014.pdf
A. Dieste, Programa de promoción de exportaciones de productor de madera, Uruguay: Dirección Nacional de Industria, Ministerio de Industria, Energía y Minería, Consejo sectorial Forestal-Maderero, 2012.
Ministerio de Industria, “Balance energético nacional,” 2023. [Online] Available: https://ben.miem.gub.uy/descargas/1balance/1-1-Libro-BEN2022.pdf.
“Data Bridge - market research,” 2022. [Online] Available: https://www.databridgemarketresearch.com/news/global-bleached-kraft-pulp-market
FAO, "Pulp and paper capacities – Survey | Capacités de la pâte et du papier - Enquête | Capacidades de pulpa y papel - Estudio 2019–2024," 2020. [Online]. Available: https://doi.org/10.4060/cb1212t
“Molded Fiber Pulp Packaging Market Size & Share by 2033.” https://www.futuremarketinsights.com/reports/moulded-fibre-pulp-packaging-market#:~:text=Molded Fiber Pulp Packaging Market Snapshot&text=The overall ten-year compound,of COVID-19 induced restrictions.. (accessed Sep. 26, 2023).
H. Sixta, Handbook of pulp, 1st ed., Germany: Wiley-VCH Verlag GmbH & Co, 2006. https://doi.org/10.1002/9783527619887
K. Kaihonen, et al., “Know Pulp,” 2022 [Online]. Available: https://www.knowpulp.com
M. A. Vivian et al., “Wood quality of Pinus taeda and Pinus sylvestris for kraft pulp production,” Sci. For., vol. 43, no. 105, pp. 183–191, 2015.
M. Akgül, Y. Çöpür, and S. Temiz, “A comparison of kraft and kraft-sodium borohydrate brutia pine pulps,” Build. Environ., vol. 42, no. 7, pp. 2586–2590, 2007. https://doi.org/10.1016/j.buildenv.2006.07.022
S. H. Yoon and A. Van Heiningen, “Kraft pulping and papermaking properties of hot-water pre-extracted loblolly pine in an integrated forest products biorefinery,” Tappi J., vol. 7, no. 7, pp. 22–27, 2008.
C. Fuenmayor and S. W. Park, “Evaluación del efecto de la carga alcalina y factor H en el pulpeo kraft de Pinus Caribaea var . hondurensis de las plantaciones de CVG-PROFORCA – Venezuela,” Copérnico, vol. 7, pp. 03–14, 2007. https://www.researchgate.net/publication/303051113
F. Huang and A. Ragauskas, “Extraction of hemicellulose from loblolly pine woodchips and subsequent kraft pulping,” Ind. Eng. Chem. Res., vol. 52, no. 4, pp. 1743–1749, 2013. https://doi.org/10.1021/ie302242h
S. D. Mansfield, K. K. Y. Wong, and A. R. Dickson, “Variation in the response of three different Pinus radiata kraft pulps to xylanase treatments,” Wood Fiber Sci., vol. 32, no. 1, pp. 105–115, 2000.
P. Martinez, “Efecto del sobre espesor de las astillas de Pinus radiata en el proceso de cocción kraft”, Master's dissertation, Universidade Federal de Viçosa, Minas Gerais, Brasil, 2012. [Online]. Available: https://www.locus.ufv.br/bitstream/123456789/5929/1/texto%20completo.pdf
S. Gharehkhani et al., “Basic effects of pulp refining on fiber properties - A review,” Carbohydr. Polym., vol. 115, pp. 785–803, 2015. https://doi.org/10.1016/j.carbpol.2014.08.047
S. K. Gulsoy and F. Ozturk, “Kraft pulping properties of european black pine cone,” Maderas Cienc. Tecnol., vol. 17, no. 4, pp. 875–882, 2016. https://doi.org/10.4067/S0718-221X2015005000076
A. Sluiter, R. Ruiz, C. Scarlata, J. Sluiter, and D. Templeton, “Determination of extractives in biomass - NREL/TP-510-42619,” National Renewable Energy Laboratory, 2008. [Online]. Available: https://www.nrel.gov/docs/gen/fy08/42619.pdf
A. Sluiter et al., “Determination of structural carbohydrates and lignin in Biomass - NREL/TP-510-42618,” National Renewable Energy Laoratory, 2008, [Online]. Available: http://www.nrel.gov/docs/gen/fy13/42618.pdf
G. Uçar and M. Balaban, “Accurate determination of the limiting viscosity number of pulps,” Wood Sci. Technol., vol. 38, no. 2, pp. 139–148, 2004, https://doi.org/10.1007/s00226-003-0218-0
P. A. Rigatto, R. A. Dedecek, and J. L. Monteiro de Matos, “Influence of soil attributes on quality of Pinus taeda wood for cellulose Kraft production,” Viçosa, vol. 28, no. 2, pp. 267–273, 2004. https://doi.org/10.1590/S0100-67622004000200013
B. Hortling, T. Tamminen, and O. Pekkala, “Effects of delignification on residual lignin-carbohydrate complexes in normal pine wood and pine wood enriched in compression wood. 1. Kraft pulping,” Nord. Pulp Pap. Res. J., vol. 16, no. 3, pp. 219–224, 2001. https://doi.org/10.3183/npprj-2001-16-03-p219-224
A. Ahmed, G. C. Myers, and S. AbuBakr, “Packaging grade kraft pulp from small-diameter softwood,” in TAPPI Pulping/Proc. Product Quality Conf., 2000, pp. 1–9.
A. Hussein, W. Gee, P. Watson, and S. Y. Zhang, “Effect of precommercial thinning on residual sawmill chip kraft pulping and pulp quality in balsam fir,” Wood Fiber Sci., vol. 38, no. 1, pp. 179–186, 2006
H. R. Motamedian, A. E. Halilovic, and A. Kulachenko, “Mechanisms of strength and stiffness improvement of paper after PFI refining with a focus on the effect of fines,” Cellulose, vol. 26, no. 6, pp. 4099–4124, 2019. https://doi.org/10.1007/s10570-019-02349-5
M. Bäckström, M. C. Kolar, and M. Htun, “Characterisation of fines from unbleached kraft pulps and their impact on sheet properties,” Holzforschung, vol. 62, no. 5, pp. 546–552, 2008. https://doi.org/10.1515/HF.2008.081
How to Cite
APA
ACM
ACS
ABNT
Chicago
Harvard
IEEE
MLA
Turabian
Vancouver
Download Citation
Recibido: 21 de agosto de 2023; Aceptado: 6 de mayo de 2024
Abstract
Context:
In Uruguay, numerous Pinus taeda plantations are at final-turn age, but they still do not have commercial destination and are exported as green-wood logs. For the development of this sector, it is necessary to strive towards a comprehensive processing of this resource.
Method:
This work focused on analyzing the use of Pinus taeda wood available in the country to produce brown kraft pulp with a kappa number of 80, which can be used to make packaging paper. As raw materials, we employed by-products from the mechanical wood-transformation industry (wood chips and thinning wood) and final-turn wood. Pulping tests were carried out, varying the alkali charge and the H-factor while aiming for a kappa number of 80. The viscosity, pulping, and rejection yield were measured in the pulps, and the pH and residual alkali content were evaluated in black liquor.
Results:
Based on the results, the best pulping conditions were an active alkali charge of 14% (Na2O) and an H-factor of 1260 for sawmill chips and thinning wood, as well as an active alkali charge of 14% (Na2O) and an H-factor of 1080 for f inal-turn wood. The pulp obtained with sawmill chips exhibited the most resistant f ibers, and the final-turn wood pulp was the most sensitive to the refining process. Under the aforementioned conditions, the paper properties of laboratory-produced pulp are comparable with those of commercial pulp.
Conclusions:
This indicates that it is technologically possible to produce brown kraft pulp from Uruguayan Pinus taeda wood, with adequate quality to produce packaging paper.
Keywords:
kraft pulp, Pinus taeda, paper properties.Resumen
Contexto:
En Uruguay existen numerosas plantaciones de Pinus taeda que están en edad de turno final, pero que aún no tienen un destino comercial y se exportan como troncos verdes. Para el desarrollo de este sector, es necesario buscar un procesamiento integral de este recurso.
Método:
Este trabajo se enfocó en analizar el uso de la madera de Pinus taeda disponible en el país en la producción de pulpa kraft marrón con un número kappa de 80, que puede utilizarse para fabricar papel de embalaje. Como materia prima, se emplearon subproductos de la industria del aserrado (chips y madera de raleo) y madera de turno final. Se realizaron ensayos de pulpeo, variando la carga de álcali y el factor H con el objetivo de alcanzar un número kappa de 80. Sobre las pulpas se midieron la viscosidad, el rendimiento del pulpeo y el rechazo, y se evaluaron el pH y el contenido de álcali residual sobre el licor negro.
Resultados:
Con base en los resultados, las mejores condiciones de pulpeo fueron una carga de álcali activo del 14% (Na2O) y un factor H de 1260 para los chips de aserradero y la madera de raleo, así como una carga de álcali activo del 14% (Na2O) y un factor H de 1080 para la madera de turno final. La pulpa obtenida con chips de aserradero presentó las fibras más resistentes, y la pulpa de madera de turno final fue la más sensible al proceso de refinado. Bajo las condiciones mencionadas, las propiedades papeleras de la pulpa producida en laboratorio son comparables con las de la pulpa comercial.
Conclusiones:
Esto indica que es tecnológicamente posible producir pulpa kraft marrón a partir de madera de Pinus taeda uruguaya, con la calidad adecuada para producir papel de embalaje.
Keywords:
kraft pulp, Pinus taeda, paper properties.Introduction
In Uruguay, the forest industry has been bolstered since the approval of the second Forest Law in 1987, increasing the area of forest plantations from 80 000 ha in 1988 to more than 1 000 000 in 2018 1. Since 2007, the production of bleached kraft pulp from eucalyptus wood has positioned itself as one of the leading markets in the country. However, the processing of pine wood is focused on the production of sawn boards and plywood in small and medium-sized production plants and in a context where wood supply widely exceeds the demand, resulting in the accumulation of this raw material 1,2. Likewise, the production yields are approximately 50%, generating 1 000 000 m3 of chips and cutouts on an annual basis. In addition to the accumulation of final-turn wood, 1 400 000 m3 of thinning wood are produced annually and are underutilized 3. Currently, this biomass is used for power generation, but, due to changes in the country’s energy matrix, including the installation of wind farms and the energy input from eucalyptus kraft pulp production mills, this alternative will not be economically sustainable in the future 4.
Ontheother hand, the consumption of packaging paper is increasing worldwide, with a compound annual growth rate (CAGR) of 2.3% in 2021 5. This is due to increases in international trade and human consumption. The rise in trade implies a greater consumption of packaging paper 6 and, consequently, an increase in the consumption of brown pulp, with the growth forecast being 4.6% by 2030 7. Additionally, there is a trend towards replacing non-removable plastic packaging with packaging made from more sustainable materials like paper
Kraft cooking is the most used pulping method worldwide due to several advantages: the good quality of the pulp produced, the fact that the recovery cycle allows operating with low replacement and onlarge production scales, and its low environmental impact in modern mills 6,8. This method focuses on dissolving lignin while preserving the highest possible fraction of cellulose and hemicellulose in the pulp. Since the objective of this work is to obtain unbleached pulp, a greater portion of lignin and hemicellulose remains in the pulp, which increases the cooking yield and improves the properties of the paper 8,9.
The main operating parameters in the kraft process are the alkali charge and the H factor. The first indicates the amount of sodium hydroxide and sodium sulfide that is added to the digester per ton of wood, and the second is a combination of time and the temperature at which the process is carried out, according to Arrhenius-type kinetics, in order to reach a predetermined value regarding the kappa number of the pulp at the digester discharge 9. For pine wood used in the production of packaging paper, the alkali charge typically varies between 15 and 20% (as Na2O), and the H factor is between 750 and 2040 10-15.
In kraft cooking, sodium hydroxide and sodium sulfide are used as active chemicals. Sodium hydroxide provides the alkaline medium for lignin solubilization, while sodium sulfide degrades lignin and makes the process more selective, as fewer amounts of hemicelluloses are solubilized. It is worth adding that the wood is chipped prior to being fed to the digester, so the shape and size of the chips determine the vaporization and impregnation performance, as well as the heat and mass transfer in the digester 8,16. The feasibility of using wood that was chipped for another purpose (chip subproducts of sawn wood) should be evaluated.
Paper properties are a set of physical, chemical, and physicochemical measurements that allow characterizing a sample of paper or cardboard. To carry out these measurements, the pulp sample is subjected to a refining process, and manual sheets are subsequently formed. The refining extension must be enough to produce fibrillation of the fibers in order to enable sheet formation, but it cannot be excessive to the point of damaging the integrity of the fibers 17.
The degree of refinement is quantified by determining drainability, which measures the interaction between fibers in forming a framework. This measurement is carried out using the Canadian Standard Freeness (CFS) method. In the industrial production of packaging paper, elongation properties are the most relevant, especially tensile strength, which depends on the length of the fibers and the links between them, and the bursting resistance, which evaluates the overall paper strength. Tear resistance is also measured as a strength property. To characterize paper, grammage, thickness, air permeability, and opacity are also usually determined 11,18.
The aim of this work was to evaluate the quality of the available Pinus taeda wood in Uruguay to produce unbleached kraft pulp, determining the pulping conditions for residues from mechanical wood processing, thinning, and final-turn wood. In addition, selected pulping conditions were used to evaluate the paper properties of the selected pulps, aiming to establish whether it is technologically possible to market them as inputs for the production of packaging paper.
Materials and method
Raw materials
Pinus taeda chips were provided by a sawmill located in the department of Rivera (Uruguay), using 24-year-old clearcut logs with an average diameter at the fine point of 40 cm. We also tested 20-year-old final-turn clearcut Pinus taeda logs with apical diameters of 54.3, 40.0, and 38.6 cm from the department of Tacuarembó (Uruguay), as well as 16-year-old wood from commercial thinning, with apical diameters of 28.2, 30.9, and 22.0 cm, also from the department of Rivera. In the last two cases, the material was chipped, and a mixture composed of three specimens and six branches was produced.
To compare the papermaking properties of this wood against available commercial samples, two samples of brown kraft pulp from Pinus radiata were used.
Drying and classification
The chips of the three types of wood were processed separately. First, they were classified in a tray sieve (Regmed 87 model CC-2, Technical Industry of Precisao Ltda., Brazil) according to the SCAN-CM 40:01 standard.
The ‘accepted chips’ were dried in a Nardi tray dryer with induced draft air circulation (12 Hz) at 40 °C for 72 h, reaching a final humidity of 8%. They were kept in a dry environment and not exposed to solar radiation until use.
Physicochemical characterization of the Wood
The basic density was determined using the TAPPI T 258 OM-16 standard. The extractives were quantified using water and ethanol as solvents 19. The extractive-free biomass was characterized in terms of carbohydrates, aliphatic acids, and acid-soluble and-insoluble lignin according to the National Renewable Energy Laboratory’s procedure (NREL) 20 ,using an HPLC instrument (Shimadzu Corporation, model LC20, Kyoto, Japan) with a refractive index and UV-visible detectors. With regard to the aforementioned procedure, it is worth noting that only the Aminex HDX-87H columna was used,with a Flow of 0.6 mL/min, a temperature of 45 °C, and 0.005 M of sulfuric acid as the mobile phase. Soluble lignin levels were measured by spectrophotometry (Shimadzu Corporation, model UVmini-1240) at a wavelength of 240 nm, considering an absorptivity of 12 L/g.cm according to the NREL procedure 20. The ash content was determined by following the TAPPI T 211 standard.
Brown kraft pulp production
Pulping tests were carried out on the chips obtained from the sawmill. Once the best conditions for these chips were established, tests were carried out in limited condition ranges on the chips from thinning and final-turn wood.
A thermostatic oil bath with eight 316 stainless steel rotating cylinder vessels was used for pulping. Each vessel had a volume of 300 mL (Fibretec model FBI PT 2002B, India). The maximum cooking temperature was fixed at 170 °C, the wood liquor ratio was 4.5:1, and the percentage of sulfidity was 30%.The alkali charge varied between 14% and19.5%(Na2O),whichwasdeterminedbyfollowingthe ISO AWI 23774 standard, and the H-factor was set at 720, 900, 1080, or 1260. The H-factor is a process control variable that expresses the cooking time and temperature in batch reactors as a single variable. Geometrically, it is the area under the relative rate of reaction vs. the time curve 8.
After cooking, the pulp was washed by hand in cloth bags. In the first instance, it was washed using three spin cycles, and a total 2 L of deionized water were used per cycle. After the last cycle, the cloth bag with the pulp remained submerged in deionized water for 24 h. After that time, a fourth washing cycle was conducted, and the pulp was stored at 4 °C until analysis.
The pulp was refined using a disc refiner (Kumagai Riki Kogyo Co., Ltd., Tokyo, Japan) until the defibrillation point was reached. This value was determined by observation under a microscope. The refiner disks were 30 cm diameter, and the gap between them was 1.12 mm.
The refined pulp was homogenized at 2000 rpm (Kumagai Riki Kogyo Co., Ltd., Tokyo, Japan) and sorted using a separating sieve (Kumagai Riki Kogyo Co., Ltd., Tokyo, Japan) with a 0.15- mm slotted plate for 20 min and under 8 kg/cm2 of water pressure.
Black liquor characterization
For the black liquor obtained after cooking, the final pH and residual alkali were determined according to the ISO AWI 23775 standard.
Pulp characterization
The pulp water content was determined by drying at 105 °C, as per the ISO 638 standard. We also calculated the cooking yield was, defined as the relation between the mass of the dry pulp obtained and the mass of the dry chips fed to the reactor. The percentage of rejected pulp was determined, defined in turn as the mass of dry rejects retained in the separating sieve in relation to the total dry pulp mass.
For the accepted pulp, the kappa number (ISO 302) and the viscosity (ISO 5351) were determined. The standard for viscosity determination applies to pulps with low lignin content (less than 5%); otherwise, dissolution in cupriethylene diamine is not completed. In order to use this standard, the literature proposes dissolution, followed by filtering the material before carrying out the measurement measuring 21.
Disaggregation of commercial pulps
Commercial samples were received in sheets with 90% dryness. These samples were separated into 2 cm2 pieces and left in distilled water for 24 h at room temperature, with a ratio of 24 g of dry pulp per L of water. The hydrated pieces were disintegrated with 2 L distilled water at 40 °C in a disintegrator pulper (Universal Engineering Corporation, model UEC-2008, India) for 15 min.
Paper properties
The pulp was refined at 6000, 9000, and 12 000 revolutions in a PFI mill (model no. 209, Hamjern, Oslo, Norway; TAPPI Test Method T 248 sp15, 2015). The drainability was determined by measuring the Canadian Standard Freeness (CSF), following the TAPPI T 227 om-17 standard. Ten manual sheets were formed per sample, according to the ISO 5264-2 and ISO 5269-2 standards, and conditioned at 23 °C and 50%humidity for at least 4 h according to the ISO 536.
The sheets were used to determine grammage, thickness, opacity, and air permeability, as per ISO 536, ISO 534, ISO 2471, and ISO 5636-5, respectively. As for the mechanical properties, tensile strength, tear resistance, and burst strength were determined by following TAPPI T 494 om-01, ISO 1974, and ISO 2758.
The resistance indices were calculated as the relationship between the resistance and the average weight of the sample at a given degree of refinement.
Calculation of uncertainties and statistical análisis
The statistical error for the structural components of the biomass was calculated as twice the standard deviation. The error for the H-factor corresponds to the contribution during ± 1 min at maximumtemperature. The error in alkali loading and residual alkali corresponds to ± 0.1 mL of titrant duringtitration. The errors of the otherparameterswerecalculatedaccordingtotherecommendationsof their corresponding standard methods. Tocomparethepaperproperties,thereportederrorwastakenas the standard deviation. Regarding statistical treatment, an ANOVA was performed while using Tukey’s test with a confidence value of 95%.The tables corresponding to the paper properties present ananalysis that considers each sample and the number of revolutions as partitions (lowercase and uppercase, respectively).
Results and discusión
Chemical characterization
85% of the sawmill by-product chips had a suitable size for use in the kraft pulping process, whereas 11% were larger and could be re-chipped.
The sawmill chips exhibited a basic density of 466 ± 2 kg/m3, while the final-turn wood reported 442 ± 10 kg/m3 and thinning Wood showed 432±6kg/m3.These values are within the range reported in the literature for Pinus taeda wood (10,22). The thinning and final-turn wood samples exhibited lower basic density values, which may be due to the fact that the samples contained branches. Branches have higher lignin content because of the reaction wood that is generated during their growth. Lignin is a hydrophobic compound, so, for the same mass of dry solid, the volume saturated in water is lower.
Table I shows the chemical composition of the three types of wood, expressed as grams per 100 grams of dry wood. Carbohydrates (cellulose and hemicelluloses) are presented as their constituent monomers. The contents of xylose, mannose, and galactose are expressed as xylose equivalents, as the chromatographic column used does not allow separating these three monomers.
Table I. : Chemical characterizationof the different Pinus taeda Woods used in this work

The three types of wood exhibited similar carbohydrate content (glucose, arabinose, xylose, mannose, and galactose). However, the sawmill chips had lower extractives and lignin contents, favoring the pulping process. The higher content of lignin and extractives in the thinning and final-turn wood could be explained by the presence of branches in the composition of the starting mixture, as mentioned above.
Sawmill chips
As previously mentioned, the selection criteria for pulping were adjusted using sawmill chips and performing kraft pulping under the conditions mentioned in section 2.4. Once the best conditions were found, a narrow search of conditions was performed for the thinning and final-turn wood.
Kraft pulping
Table II shows the results obtained for the different pulping conditions of the sawmill chips.
Table II.: Properties othe pulps obtained after applying different conditions to the sawmill Wood chips

The yield values obtained (50-65% for a kappa number greater tan 68 and 40-50% for a kappa number of less tan 68) are similar to those reported in the literatura and are consistent with the characteristics of the process 10-15. Note that, the higher the degree of delignification, the lower the residual lignin content- thus, a lower kappa number can be obtained. This also entails a greater loss of carbohydrates, which further contributes to the decrease in yield. If the variation of the kappa number is analyzed within the same H-factor range, the expected trend is obtained. This is because, when the alkaline load decreases, the kappa number and the yield increase.
The percentage of rejection for the samples with a kappa number between 70 and 80 was within the expected range (0.9-6.9%). However, the tests with more severe pulping conditions reported a lower rejection percentage, corresponding to a higher degree of delignification (which can be seen as a lower kappa number). Nevertheless, there were samples (such as number 10) that deviated from the general trend. It is worth stating that a greater delignification decreases the rigidity of the matrix, which makes the mechanical refining stage more effective, resulting in a lower number of fiber bundles retained in the screening stage.
In the viscosity analysis, the expected trend was not found, since the increment in the alkali load produced greater carbohydrate degradation and a decrease in the degree of polymerization. However, the viscosity value increased. This could be explained by the experimental procedure used; due to the high lignin content, the tested samples did not completely dissolve in the cupriethylene diamine. In the samples with lower lignin contents (i.e., a lower kappa number), the dissolved material in the cupriethylene diamine was higher, since cellulose was more available. Consequently, the viscosity value increased. Therefore, only samples with similar kappa numbers should be compared. In these cases, the viscosity value increased when the alkali load decreased, and the H-factor increased, which was the expected trend. It can be concluded that, for samples with a similar kappa number, those that were produced with a lower alkali load exhibited a higher viscosity 8,21.
Considering the results reported in Table II, tests 7 (H-factor: 1077; alkali load: 16.0% Na2O) and 10 (H-factor: 1268; alkali load 14.0% Na2O) were selected as the best conditions, given that, out of the samples with a kappa number in the range of 80, they reported the highest yields and viscosity values, as well as a lower rejection content.
Black liquor
In all the tests carried out, the final pH of the black liquor showed values greater than 11. Thus, there was no risk of lignin precipitation. The samples that reported values of residual active alkali (RA) within the recommended range (2-4 g/L as Na2O) were numbers 6, 7, and 11. Considering the RA recommended by the literature and the volume used in each test, the recommended value was 0.48 to 0.96 g as Na2O. The samples with an RA of less than 0.96 g as Na2O exhibited a higher degree of polymerization, and, consequently, they yielded pulp of better quality 8.
Thinning and final-turn Wood
The thinning and final-turn wood samples were analyzed using test 10, which was selected because it demonstrated the lowest active alkali consumption among the two best conditions. Under these conditions, a kappa number of 72.0±0.9 was reached with the final-turn wood. In order to reach the target kappa number of 80, the same active alkali charge was used, and the H-factor decreased (H-factor: 1077; alkali load: 14% as Na2O). This could be explained by the presence of compression wood in the sample composition 23.
Table III shows the results for the thinning and final-turn wood, as well as for the sawmill chips obtained with the same active alkali load and the highest H-factor.
Table III: Results for the kraft pulping of thinning and final-turn wood when compared to sawmill chip woodunder similar pulping conditions

The pulping yields, using 14% active alkali (Na2O), were similar for the three types of wood. Likewise, in all cases, the percentage of rejection was within the expected range, as reported by other authors 24,25.
On the other hand, the viscosity values of the pulps obtained from thinning and final-turn wood were higher than those from sawmill chips. In the case of the final-turn wood, the high viscosity was likely due to the lower H-factor used, which implies less severe cooking conditions and, therefore, less attacking of the cellulose chains. As for the thinning wood, a higher rejection value was obtained. Thus, more severe conditions would be needed to match the degree of cooking of the sawmill chip wood. The thinning wood’s lower degree of cooking was also reflected in a higher viscosity value.
Commercial pulp simples
The commercial samples, called commercial sample 1 (CS1) and commercial sample 2 (CS2), exhibited relatively low kappa numbers (CS1: 33±3 and CS2: 40±4, respectively). In addition, comparable viscosity values were obtained (973±4 mL/ g for CS1 and 882±4 mL/ g for CS2) with respect to the first two samples in Table III. Laboratory pulps with lower viscosity than the commercial ones were obtained at similar kappa numbers. This behavior has been previously observed in our work group, and it could be attributed to the fact that laboratory-scale equipment is considerably smaller than industrial pulping reactors; the former has a higher metal-surface- to-pulp ratio than the latter. Therefore, there was a greater deterioration of the fiber in contact with the metal wall.
Paper properties
This section outlines the paper properties achieved with the different studied pulps. The pulps were refined at different revolutions, as indicated in Section 2. The different properties measured at each revolution are shown in the figures, as well as the trends observed. The notation used is as follows: AA14 (sawmill chip wood; alkali charge: 14% as Na2O; H-factor: 1260), AA16 (sawmill chip wood; alkali charge: 16%asNa2O;H-factor:1080),FTW(finalturnwood;alkalicharge:14%asNa2O;H-factor: 1080), TW(thinning wood; alkali charge: 14% as Na2O; H-factor: 1260), CS1 (commercial sample 1), CS2 (commercial sample 2).
Drainability
The drainability was quantified by measuring the CSF, as shown in Fig. 1.
Figure 1: Drainability (mL) according to CSF measurements for four laboratory pulps and two commercial brown pulps
The results showed the expected trend: drainability values decreased when refining increased due to the fibrillation phenomenon 17. Sample AA14 exhibited the highest drainability values for all the revolutions tested. Thus, it was considered to be the fiber with the least damage.
Air permeability
Fig. 2 shows the air permeability values, which increased for all samples as the number of revolutions increased. The reason for this is that the higher the refinement, the greater the fibrillation. Therefore, the sheets produced with more refined pulps were more compact and less porous. When partitioning by sample, a statistically significant difference between the three refining points was found, except for the thinning sample, which reported no significative difference between 9000 and 12 000 revolutions. When partitioning by degree of refinement, it was observed that, at 9000 and 12 000 revolutions, sample AA14 was the least porous, which agreed with the previous result, exhibiting the lowest drainability values. This implies that sample AA14 is the most resistant fiber to mechanical treatment.
Figure 2: Air permeability (s) values for the sheets evaluated with the different samples at different PFI revolutions. Lowercase letters are used to compare different samples with the same PFI revolutions. Capital letters are used to compare the same pulp at different PFI revolutions. The same letter indicates no statistical differences between the samples.
Opacity
The opacity value (Fig. 3) decreased as the number of revolutions increased. This behavior was expected, as the sheets were more compact when the opacity decreased. This could be explained by the external fibrillation generated during the refinement of the pulp produced with a more closed framework, wherein fines were generated, filling the spaces between the fibers. When partitioning by samples, the statistical analysis showed statistically significant differences for samples AA14 and TW at 6000 revolutions, as well as for samples CS2 and FTW at 12 000 revolutions, for which no trend was evident.
Figure 3: Opacity (%). Lowercase letters are used to compare different samples with the same PFI revolutions. Capital letters are used to compare the same pulp at different PFI revolutions. The same letter indicates no statistical differences between samples.
Tear resistance index
According to the values presented in Fig. 4, the tear strength index value decreased as the number of revolutions increased, possibly due to the deterioration of the fiber due to mechanical action. At 6000 revolutions, samples AA14 and AA16 reported a higher tear strength index value. The same trend was maintained for the different degrees of refinement, meaning that these samples had the longest fiber length. This could be explained by the fact that samples AA14 and AA16 corresponded to the older specimens.
Except for sample AA14, no statistically significant difference was observed at 9000 and 12 000 revolutions when partitioning by sample; increasing the refining process did not cause perceptible damage to the analyzed pulps.
Figure 4: Tear resistance index (mN/(g/m2)). Lowercase letters are used to compare different samples with the same PFI revolutions. Capital letters are used to compare the same pulp at different PFI revolutions. The same letter indicates no statistical differences between samples.
Tensile strength index
Fig. 5 shows the tensile strength indices for different levels of refinement. These values increased with the number of revolutions because the external fibrillation phenomenon produced during refinement generates a greater number of resistant bonds (26). When partitioning by sample, a similar behavior was observed in the opacity measures. hus, the trend was not clear. When partitioning by degree of refinement, at 6000 revolutions, there was no statistically significant difference between the samples. However, for higher refinement revolutions, the samples were differentiated, with the f inal-turn pulp having the best response to the process.
Figure 5: Tensile strength index (N/(g/m2)). Lowercase letters are used to compare different samples with the same PFI revolutions. Capital letters are used to compare the same pulp at different PFI revolutions. The same letter indicates no statistical differences between samples.
Bursting strength index
The values obtained for this index are shown in Fig 6. Although the distribution of errors of the experimental measurements didnotallowforstatistical analysis, the resistance values obtained with the experimental samples were similar to each other as well as to those obtained from commercial pulps. This measure is similar to that reported by other authors 27.
Figure 6: Bursting strength index(kPa/(g/m2)).Lowercaseletters areusedtocomparedifferentsamples with the same PFI revolutions. Capital letters are used to compare the same pulp at different PFI revolutions. The same letter indicates no statistical differences between samples.
Conclusions
Based on the experimental data, sawmill by-product chips were found to be a viable raw material for use in a kraft pulp mill. Out of the sawmill chips used, 85% had a suitable size for use as raw, while 11%werelarger and could be re-chipped.
The three types of wood tested exhibited similar chemical compositions and small differences in their basic density and lignin contents, which could be explained by the presence of branches in the composition of the composite mixture.
It was possible to obtain pulp with a kappa number of 80 under an active alkali charge of 14% (Na2O) and an H-factor of 1260 for sawmill chips and thinning wood, as well as 14% (Na2O) and an H-factor of 1080 for final-turn wood. These pulping conditions resembled those reported in the literature, in addition to the yields and the rejection values obtained. However, the viscosity values were lower than expected.
This difference could be explained by the differences between the methods used, as our measurements were outside the standard method conditions.
Sample AA14, which corresponds to sawmill chips pulped with a 14% acetic alkali charge (Na2O) and an H-factor of 1080, exhibited the best quality in terms of paper properties, with the highest CSF andtear index values. Likewise, the final-turn sample was shown to be the most sensitive to the refining process, reporting the lowest tear resistance indices and the most compact sheets.
In this vein, it can be stated that the brown kraft pulp produced with the Pinus taeda wood available in Uruguay exhibits adequate quality and can be marketed as an input to produce packaging paper.
The results obtained in this research confirm the technological feasibility to produce Pinus taeda brown kraft pulp mill. In the future, an economic and environment study could be conducted to determine the feasibility of installing an industrial-size mill in Uruguay
Acknowledgements
Acknowledgements
The authors would like to thank DANK S.A. and Eng. Carlos Montero for kindly providing the pine chips and logs; the Graduate Academic Commission (Comisión Académica de Posgrado, CAP) for the postgraduate scholarship of Viviana Palombo (BDMX_2020_1#49478137); and the Technological Laboratory of Uruguay (Laboratorio Tecnológico del Uruguay, LATU) for providing support equipment.
References
License
Copyright (c) 2024 Viviana Palombo, Leonardo Clavijo, Maria Noel Cabrera

This work is licensed under a Creative Commons Attribution-NonCommercial-ShareAlike 4.0 International License.
From the edition of the V23N3 of year 2018 forward, the Creative Commons License "Attribution-Non-Commercial - No Derivative Works " is changed to the following:
Attribution - Non-Commercial - Share the same: this license allows others to distribute, remix, retouch, and create from your work in a non-commercial way, as long as they give you credit and license their new creations under the same conditions.